SEARCH
Search Details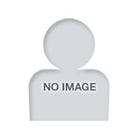
YAMAMOTO Hiroshi
Mechanical Science Division | Professor |
Department of Mechanical Engineering and System Design |
Researcher information
■ Degree■ Research Keyword
■ Field Of Study
- Informatics, Mechanics and mechatronics
- Manufacturing technology (mechanical, electrical/electronic, chemical engineering), Machine elements and tribology
- Manufacturing technology (mechanical, electrical/electronic, chemical engineering), Design engineering
- 1986, Tokyo Institute of Technology, Science of Engineering, Japan
- 1984, Tokyo Institute of Technology, School of Engineering, Japan
Performance information
■ Paper- Estimation of characteristics of supported object on vibration isolator using air suspensions
Kenta NAKANO; Hiroshi YAMAMOTO; Terumasa NARUKAWA
Transactions of the JSME (in Japanese), Volume:91, Number:942, First page:24, Last page:00218, Feb. 2025, [Reviewed], [Corresponding]
Japan Society of Mechanical Engineers, Japanese, Scientific journal
DOI:https://doi.org/10.1299/transjsme.24-00218
DOI ID:10.1299/transjsme.24-00218, eISSN:2187-9761, 共同研究・競争的資金等ID:45256611 - Development of a vibration isolation system using an air suspension with automatic damping adjustment mechanism
Yuki TAKANAMI; Hiroshi YAMAMOTO; Terumasa NARUKAWA
Transactions of the JSME (in Japanese), Volume:89, Number:924, First page:23, Last page:00096, Aug. 2023, [Reviewed], [Corresponding]
Japan Society of Mechanical Engineers, Japanese, Scientific journal
DOI:https://doi.org/10.1299/transjsme.23-00096
DOI ID:10.1299/transjsme.23-00096, eISSN:2187-9761, 共同研究・競争的資金等ID:45256611
- Effect of Bolted Joint Layer on the Vibration Characteristics of Spindle Rotor
YAMAMOTO Hiroshi; ZHENG Ying; NUMAZAKI Tomohiro
Transactions of the Japan Society of Mechanical Engineers C, Volume:74, Number:742, First page:1432, Last page:1437, 2008
This paper describes an investigation of the effect of joint layer on the vibration characteristics of a spindle rotor. The test rotor is composed of a journal part and two thrust plates bound with bolts. Each thrust plate and a journal part are clamped with eight M4 bolts which are arranged on the circle at 45 degrees intervals with a uniform clamping torque. The each surface of bolted joints is processed by two methods in order to change the roughness or roundness of surface. In this paper, we consider the lower three bending vibration mode of the spindle. In all conditions of surface of joint layer, natural frequencies increase and damping ratios decrease as the clamping torque of each bolt increases. On the other hands, in all condition of clamping torque, natural frequencies increase and damping ratios decrease as the roughness and roundness of surface decreases. Moreover, we can decrease the resonance amplitude by increasing clamping torque, decreasing roughness and roundness of surface.
The Japan Society of Mechanical Engineers, Japanese
DOI ID:10.1299/kikaic.74.1432, ISSN:0387-5024, CiNii Articles ID:110006793579, CiNii Books ID:AN00187463 - Equivalent Stiffness of Bolted Joint Layer of a Spindle Rotor
YAMAMOTO Hiroshi; ZHENG Ying; NUMAZAKI Tomohiro
Transactions of the Japan Society of Mechanical Engineers C, Volume:74, Number:743, First page:1702, Last page:1709, 2008
This paper describes an investigation of equivalent stiffness of a joint layer of a spindle rotor. The test rotor is composed of a journal part and two thrust plates bound with bolts. The each thrust plate and the journal part are clamped with eight M 4 bolts which are arranged on the circle at 45 degrees intervals with a uniform clamping torque. The each surface of bolted joints is processed by two methods in order to change the roughness of surface. We propose the identify procedure of the equivalent stiffnesses of the joint layer in normal and tangential direction based on the modal analysis theory and we can identify the equivalent stiffness in two surface conditions of joint layer. By using the identified equivalent stiffnesses, we can calculate natural frequencies of higher order which are not used in the identified procedure and the calculated ones are fairly good well with the measured natural frequencies of higher order. In two surface conditions of the joint layer, the normal stiffness and the tangential stiffness increase as the clamping torque of each bolt increases. On the other hands, in all condition of clamping torque, the normal stiffness and the tangential stiffness increase as the roughness of surface decreases. Moreover, the ratio of the tangential stiffness to the normal stiffness decreases as the surface of ronghness decreases.
The Japan Society of Mechanical Engineers, Japanese
DOI ID:10.1299/kikaic.74.1702, ISSN:0387-5024, CiNii Articles ID:110006836826, CiNii Books ID:AN00187463 - Optimum Design Method for a Two Degree of Freedom System Supported with Air Suspensions
YAMAMOTO Hiroshi; ZHENG Ying; OKADA Jun-ichi
Transactions of the Japan Society of Mechanical Engineers C, Volume:74, Number:741, First page:1129, Last page:1136, 2008
In this study we propose a design procedure of two degree of freedom system supported with air suspensions with viscous restrictions and a reservoir tanks. We use two design concepts of minimizing resonance amplitude and minimizing standard deviation of amplitude against external disturbance random vibrations of foundation. To minimize resonance amplitude, the damping ratio, which corresponds to the restriction coefficient of viscous restriction, has to be chosen in order to equalize the resonance amplitude under the condition of parallel oscillating to that under the condition of rotating oscillating. To minimize standard deviation of amplitude of the system, the optimum damping ratio which minimize the standard deviation of amplitude of the system under the condition of rotating oscillating has to be chosen when the natural frequency of the parallel mode is lower than that of the rotating mode. The optimum damping ratio which minimize the standard deviation of amplitude of the system under the condition of parallel oscillating has to be chosen when the natural frequency of the rotating mode is lower than that of the parallel mode.c
The Japan Society of Mechanical Engineers, Japanese
DOI ID:10.1299/kikaic.74.1129, ISSN:0387-5024, CiNii Articles ID:110006685250, CiNii Books ID:AN00187463 - Effects of Restriction Characteristics on Characteristics of Air Suspension
YAMAMOTO Hiroshi; ZHENG Ying; OKUMOTO Shingo
Transactions of the Japan Society of Mechanical Engineers C, Volume:74, Number:739, First page:521, Last page:528, 2008
In this study we make clear the characteristics of an air suspension with a flow channel connected from a cylinder to a reservoir tank. The flow resistance of channel is given by a viscous restriction or an orifice restriction. Differences between approximated analytical results, which are based on the 3-element model, of stiffness and damping coefficients of the air suspension with the viscous restriction and results of numerical analysis considering non-linear characteristics are very small. Moreover, the approximated analytical results of a transfer function of the air suspension and the experimental results of it are good well. Dependence of the oscillating amplitude on the maximum value of the transfer function of the air suspension system with the viscous restriction is very small since dependence of the oscillating amplitude on the stiffness and the damping is almost negligible. However, it depends on the oscillating amplitude of air suspension system with the orifice restriction because the damping coefficient of that decreases when the oscillating amplitude decreases. We can choose the optimal restriction coefficient of viscous restriction to minimize resonance amplitude easily. However, it is difficult to choose the optimal restriction coefficient of orifice restriction to minimize resonance amplitude because the oscillating amplitude often fluctuates generally. Thus, the air suspension with the viscous restriction is better for isolating the small vibration, in case of the high precision machinery.
The Japan Society of Mechanical Engineers, Japanese
DOI ID:10.1299/kikaic.74.521, ISSN:0387-5024, CiNii Articles ID:110006643663, CiNii Books ID:AN00187463 - Optimum Design Method of Air Suspension with Viscous Restriction
YAMAMOTO Hiroshi; ZHENG Ying
Transactions of the Japan Society of Mechanical Engineers C, Volume:74, Number:739, First page:529, Last page:535, 2008
In this study we propose a design procedure of an air suspension with a viscous damping restriction and a reservoir tank. We use two design concepts of minimizing resonance amplitude and minimizing standard deviation of amplitude against external disturbance random vibrations of foundation. In order to reducing resonance amplitude and standard deviation of amplitude, it is necessary to increase the volume ratio of the reservoir tank to the main cylinder. In these case, we can choose the optimum damping ratio which corresponds to the restriction coefficient of viscous restriction to minimize resonance amplitude or standard deviation of amplitude. As the volume ratio becomes larger, the difference between the optimum damping ratio which provides minimum resonance amplitude and what provides minimum standard deviation of amplitude becomes larger. However, we can realize the air suspension whose standard deviation of amplitude is relatively small although we choose the volume ratio and the damping ratio to minimize the resonance amplitude.
The Japan Society of Mechanical Engineers, Japanese
DOI ID:10.1299/kikaic.74.529, ISSN:0387-5024, CiNii Articles ID:110006643664, CiNii Books ID:AN00187463 - An Experimental Study of Shaft Response Characteristics of Floating Bush Hydrostatic Gas Bearing with an External Damping
MIYAJI Ryutaro; HAYASHI Takashi; YAMAMOTO Hiroshi
Journal of the Japan Society of Precision Engineering, Volume:74, Number:8, First page:841, Last page:845, 2008
In this paper, the shaft response characteristics of a floating bush hydrostatic gas bearing with an external damping (fluid damper) are investigated. The damping coefficients of fluid damper are defined by the damper clearance and the fluid viscosity. Several kinds of silicone oil, each of which is of different viscosity, are used as the damper fluid. When an impact force acts on the rotor, the rotor response generally shows under-damping. When the damping coefficients of fluid damper increase, the rotor response shows a change from under-damping to over-damping vibrations. Therefore, using the fluid damper can shorten the settling time of the rotor to about 2 natural period (5ms) of fundamental vibrations. The respective settling times for the rotor and the floating bush are almost the same. The optimum damping coefficient of fluid damper is set around 1. of damping factor in the fixed bush - floating bush bearing system.
The Japan Society for Precision Engineering, Japanese
DOI:https://doi.org/10.2493/jjspe.74.841
DOI ID:10.2493/jjspe.74.841, ISSN:0912-0289, CiNii Articles ID:110006865143, CiNii Books ID:AN1003250X - スピンドルロータの振動特性にボルト締結部が及ぼす影響
山本浩,鄭頴; 沼崎知宏
日本機械学會論文集. C編, Volume:74, Number:742, First page:1432, Last page:1437, 2008
This paper describes an investigation of the effect of joint layer on the vibration characteristics of a spindle rotor. The test rotor is composed of a journal part and two thrust plates bound with bolts. Each thrust plate and a journal part are clamped with eight M4 bolts which are arranged on the circle at 45 degrees intervals with a uniform clamping torque. The each surface of bolted joints is processed by two methods in order to change the roughness or roundness of surface. In this paper, we consider the lower three bending vibration mode of the spindle. In all conditions of surface of joint layer, natural frequencies increase and damping ratios decrease as the clamping torque of each bolt increases. On the other hands, in all condition of clamping torque, natural frequencies increase and damping ratios decrease as the roughness and roundness of surface decreases. Moreover, we can decrease the resonance amplitude by increasing clamping torque, decreasing roughness and roundness of surface.
The Japan Society of Mechanical Engineers, Japanese
DOI ID:10.1299/kikaic.74.1432, ISSN:0387-5024, CiNii Articles ID:110006793579, CiNii Books ID:AN00187463 - スピンドルロータのボルト締結部における等価剛性
山本浩,鄭頴; 沼崎知宏
日本機械学會論文集. C編, Volume:74, Number:743, First page:1702, Last page:1709, 2008
This paper describes an investigation of equivalent stiffness of a joint layer of a spindle rotor. The test rotor is composed of a journal part and two thrust plates bound with bolts. The each thrust plate and the journal part are clamped with eight M 4 bolts which are arranged on the circle at 45 degrees intervals with a uniform clamping torque. The each surface of bolted joints is processed by two methods in order to change the roughness of surface. We propose the identify procedure of the equivalent stiffnesses of the joint layer in normal and tangential direction based on the modal analysis theory and we can identify the equivalent stiffness in two surface conditions of joint layer. By using the identified equivalent stiffnesses, we can calculate natural frequencies of higher order which are not used in the identified procedure and the calculated ones are fairly good well with the measured natural frequencies of higher order. In two surface conditions of the joint layer, the normal stiffness and the tangential stiffness increase as the clamping torque of each bolt increases. On the other hands, in all condition of clamping torque, the normal stiffness and the tangential stiffness increase as the roughness of surface decreases. Moreover, the ratio of the tangential stiffness to the normal stiffness decreases as the surface of ronghness decreases.
The Japan Society of Mechanical Engineers, Japanese
DOI ID:10.1299/kikaic.74.1702, ISSN:0387-5024, CiNii Articles ID:110006836826, CiNii Books ID:AN00187463 - 空気ばねで支持された2自由度系の最適設計
山本浩,鄭頴; 岡田淳一
日本機械学會論文集. C編, Volume:74, Number:741, First page:1129, Last page:1136, 2008
In this study we propose a design procedure of two degree of freedom system supported with air suspensions with viscous restrictions and a reservoir tanks. We use two design concepts of minimizing resonance amplitude and minimizing standard deviation of amplitude against external disturbance random vibrations of foundation. To minimize resonance amplitude, the damping ratio, which corresponds to the restriction coefficient of viscous restriction, has to be chosen in order to equalize the resonance amplitude under the condition of parallel oscillating to that under the condition of rotating oscillating. To minimize standard deviation of amplitude of the system, the optimum damping ratio which minimize the standard deviation of amplitude of the system under the condition of rotating oscillating has to be chosen when the natural frequency of the parallel mode is lower than that of the rotating mode. The optimum damping ratio which minimize the standard deviation of amplitude of the system under the condition of parallel oscillating has to be chosen when the natural frequency of the rotating mode is lower than that of the parallel mode.c
The Japan Society of Mechanical Engineers, Japanese
DOI ID:10.1299/kikaic.74.1129, ISSN:0387-5024, CiNii Articles ID:110006685250, CiNii Books ID:AN00187463 - 空気ばねの特性に絞り特性が及ぼす影響
山本浩,鄭頴; 奥本眞吾
日本機械学會論文集. C編, Volume:74, Number:739, First page:521, Last page:528, 2008
DOI:https://doi.org/10.1299/kikaic.74.521
DOI ID:10.1299/kikaic.74.521, ISSN:0387-5024, CiNii Articles ID:110006643663 - 粘性絞りを有する空気ばねの最適設計
山本浩,鄭頴
日本機械学會論文集. C編, Volume:74, Number:739, First page:529, Last page:535, 2008
DOI:https://doi.org/10.1299/kikaic.74.529
DOI ID:10.1299/kikaic.74.529, ISSN:0387-5024, CiNii Articles ID:110006643664 - 外部減衰を付加した浮動ブシュ静圧気体軸受の軸の応答特性の実験的研究
宮地隆太郎; 林孝,山本浩
精密工学会誌, Volume:74, Number:8, First page:841, Last page:845, 2008
In this paper, the shaft response characteristics of a floating bush hydrostatic gas bearing with an external damping (fluid damper) are investigated. The damping coefficients of fluid damper are defined by the damper clearance and the fluid viscosity. Several kinds of silicone oil, each of which is of different viscosity, are used as the damper fluid. When an impact force acts on the rotor, the rotor response generally shows under-damping. When the damping coefficients of fluid damper increase, the rotor response shows a change from under-damping to over-damping vibrations. Therefore, using the fluid damper can shorten the settling time of the rotor to about 2 natural period (5ms) of fundamental vibrations. The respective settling times for the rotor and the floating bush are almost the same. The optimum damping coefficient of fluid damper is set around 1. of damping factor in the fixed bush - floating bush bearing system.
The Japan Society for Precision Engineering, Japanese
DOI:https://doi.org/10.2493/jjspe.74.841
DOI ID:10.2493/jjspe.74.841, ISSN:0912-0289, CiNii Articles ID:110006865143, CiNii Books ID:AN1003250X - Influence of Atomospheric Gas upon Seizure of Gas Bearings
Karpov P; Harada M; Tsukazaki T; Yamamoto H
Volume:9, First page:105, Last page:109, 2004 - Influence of Atomospheric Gas upon Seizure of Gas Bearings
Karpov P; Harada M; Tsukazaki T; Yamamoto H
Applied Mechanics and Engineering, Volume:9, First page:105, Last page:109, 2004 - 最大の動剛性を有する静圧エアスピンドルの設計
山本浩; 小野京右; 崔長植; 都築正浩
Volume:63, Number:608, First page:1342, Last page:1349, 1997
DOI:https://doi.org/10.1299/kikaic.63.1342
DOI ID:10.1299/kikaic.63.1342 - 最大の動剛性を有する静圧エアスピンドルの設計
山本浩; 小野京右; 崔長植; 都築正浩
日本機械学會論文集. C編, Volume:63, Number:608, First page:1342, Last page:1349, 1997
DOI:https://doi.org/10.1299/kikaic.63.1342
DOI ID:10.1299/kikaic.63.1342, CiNii Articles ID:10007784752 - ロータの弾性変形を考慮した静圧エアスピンドルの振動解析
山本浩; 小野京右; 崔長植; 都築正浩
Volume:62, Number:603, First page:4294, Last page:4301, 1996
DOI:https://doi.org/10.1299/kikaic.62.4294
DOI ID:10.1299/kikaic.62.4294, ISSN:0387-5024, CiNii Articles ID:110002382398 - ロータの弾性変形を考慮した静圧エアスピンドルの振動解析
山本浩; 小野京右; 崔長植; 都築正浩
日本機械学會論文集. C編, Volume:62, Number:603, First page:4294, Last page:4301, 1996
DOI:https://doi.org/10.1299/kikaic.62.4294
DOI ID:10.1299/kikaic.62.4294, ISSN:0387-5024, CiNii Articles ID:110002382398 - Design and Manufacture of High-Performance Hydrostatic Air Bearing Spindle with Grid-Shaped Grooves
ONO Kyousuke; YAMAMOTO Hiroshi; UEMOTO Hiroki
Transactions of the Japan Society of Mechanical Engineers. Series C., Volume:61, Number:581, First page:220, Last page:227, 1995
This paper describes the design and manufacture of a new hydrostatic air bearing spindle with grid-shaped grooves that can provide a relatively high damping ratio in a high-frequency region of resonance, as well as high stiffness. The numbers of inner grooves on the inner surfaces of the thrust, angular and radial bearings are determined so that gas film damping becomes maximum near the natural frequencies of the thrust and radial vibration modes. Increases in groove number and groove depth generally result in high damping in the high-frequency region, but excessive increases cause damping to be negative in the low-frequency region. The design procedure to determine the optimal value of the groove parameters is described by the design charts based on numerical calculation. From the evaluation of the manufactured prototype, it is proved that the proposed air bearing spindle can realize relatively high damping ratios of thrust, angular and radial modes of 0.07, 0.11 and 0.15, respectively, while maintaining high static stiffnesses of 627 N/μm and 99 N/μm in the thrust and radial directions, respectively.
The Japan Society of Mechanical Engineers, Japanese
DOI ID:10.1299/kikaic.61.220, ISSN:0387-5024, CiNii Articles ID:110002381622, CiNii Books ID:AN00187463 - Stusy on Dynamic Characteristics and Optimal Design Method of Externally Pressurized Annular Porous Thrust Bearings (Numerical Analysis for a Porous Bearing Model with Orifice-Restricted Thin Surface Layer)
ONO Kyosuke; CUI Changzhi; YAMAMOTO Hiroshi
Transactions of the Japan Society of Mechanical Engineers. Series C., Volume:61, Number:584, First page:1626, Last page:1633, 1995
We numerically analyzed dynamic characteristics of an aerostatic annular porous thrust bearing model which has a thin choked porous surface. It is found that the choked surface causes such important and indispensable effects that can increase stiffness and shift the positive extreme values of damping from the high-frequency region to a lower frequency region, reducing negative damping in the low-frequency region. Under the conditions of allowable static stiffness and the minimum dynamic stiffness, we obtained the unique relationships between design parameters and squeeze number that provide the maximum damping ratio. Considering the mass parameter of a supported body, we propose an optimal design method to maximize damping ratio at natural frequency while maintaining stiffness in the low-frequency region.
The Japan Society of Mechanical Engineers, Japanese
DOI ID:10.1299/kikaic.61.1626, ISSN:0387-5024, CiNii Articles ID:110002381828, CiNii Books ID:AN00187463 - 多孔質環状スラスト静圧気体軸受の動特性と最適設計に関する研究(表面目づまりのオリフィス絞り効果と多孔質材内の抵抗を考慮した解析)
Kyosuke Ono; Changzhi Cui; Hiroshi Yamamoto
日本機械学會論文集. C編, Volume:61, Number:584, First page:1626, Last page:1633, 1995
We numerically analyzed dynamic characteristics of an aerostatic annular porous thrust bearing model which has a thin choked porous surface. It is found that the choked surface causes such important and indispensable effects that can increase stiffness and shift the positive extreme values of damping from the high-frequency region to a lower frequency region, reducing negative damping in the low-frequency region. Under the conditions of allowable static stiffness and the minimum dynamic stiffness, we obtained the unique relationships between design parameters and squeeze number that provide the maximum damping ratio. Considering the mass parameter of a supported body, we propose an optimal design method to maximize damping ratio at natural frequency while maintaining stiffness in the low-frequency region.
The Japan Society of Mechanical Engineers, Japanese
DOI ID:10.1299/kikaic.61.1626, ISSN:0387-5024, CiNii Articles ID:110002381828, CiNii Books ID:AN00187463 - Fundamental Study on Damping Characteristics of Externally Pressurized Porous Gas Bearing : Analysis of Annular Thrust Bearing with Orifice and Capillary Models
Cui Changzhi; Ono Kyosuke; Yamamoto Hiroshi
Transactions of the Japan Society of Mechanical Engineers. Series C., Volume:60, Number:573, First page:p1775, Last page:1782, May 1994
An externally pressurized porous gas bearing is known to provide high stiffness. Although damping is also important to realize a high-dynamic-stiffness bearing, few studies have been done on the damping characteristics and their relationships to the stiffness and static characteristics of a porous bearing. This paper reports on the analytical investigation of an externally pressurized porous annular thrust gas bearing using the orifice and capillary models from the aspect of improving its damping characteristics. It is found that stiffness and damping are determined only by the static stiffness, the reaction force of gas film and the ratio of squeeze number to the squeeze number at which damping takes an extreme value. It is also found that the damping ratio ζ is determined only by the ratio of squeeze numbers and the ratio of the static stiffness to the reaction force of gas film. Approximated simple formulas representing the relationship between dynamic quantities and static quantities are presented. The validity of the simple formulas is confirmed in a practical range of design parameters by comparison with the results of numerical calculation.
The Japan Society of Mechanical Engineers, Japanese
ISSN:0387-5024, CiNii Articles ID:110002378239, CiNii Books ID:AN00187463 - Dynamic Characteristics of Hydrostatic Air Slider with Comb-Shaped Grooves
Yamamoto Hiroshi; Ono Kyosuke
Transactions of the Japan Society of Mechanical Engineers C, Volume:59, Number:565, First page:2804, Last page:2811, 1993
In this study we develop a new hydrostatic air bearing slider with comb-shaped grooves which can provide high damping ratio in the high-frequency region of resonance, as well as high stffness. The basic idea to increase the air film damping at a high frequency region is to reduce the compressive effect of the air film by a set of parallel inner grooves. Increases in groove number and groove depth generally result in high damping in the high-frequency region, but excessive increases cause negative damping in the low-frequency region. The design procedure to determine the optimal value of the groove parameters is described by the design charts based on numerical calculation. The developed air slider has a high static stiffness of 418 N/μm (non-dimensional stiffness is 0.59) in the vertical direction, Damping ratios are 0.19, 0.12 and 0.07 at the natural frequencies of the roll, pitch and vertical vibration modes, respectively.
The Japan Society of Mechanical Engineers, Japanese
DOI ID:10.1299/kikaic.59.2804, ISSN:0387-5024, CiNii Articles ID:110002392993, CiNii Books ID:AN00187463
- The Japan Society of Precision Engineering
- Japanese Society of Tribologists
- The Japan Society of Mechanical Engineers
- 積載物および走行路面の状況に自動的に対応する無人搬送車用防振システムの開発
01 Apr. 2021 - 31 Mar. 2024
Grant amount(Total):4290000, Direct funding:3300000, Indirect funding:990000
Grant number:21K03943
論文ID:49599703 - Development of a high presision vibration isolator using air suspensions with auto tuning mechanism
Japan Society for the Promotion of Science, Grants-in-Aid for Scientific Research, Grant-in-Aid for Scientific Research (C), 01 Apr. 2016 - 31 Mar. 2020
Yamamoto Hiroshi, Saitama University
Grant amount(Total):4810000, Direct funding:3700000, Indirect funding:1110000
For the purpose of developing a high precision vibration isolator using air suspensions with an automatic adjustment mechanism, we firstly clarify the dynamic characteristics of the vibration isolator supported by multiple air suspensions theoretically and experimentally. The design guideline for minimizing the resonance magnification of the vibration isolator is clarified. In addition, in order to clarify the effect of load fluctuation, the effect of the supporting mass and the position of the center of gravity on the dynamic characteristics of the vibration isolator supported by the air suspensions is clarified. We find that it is necessary to adjust the equivalent damping coefficient of the air suspension in order to minimize the resonance amplitude when the load changes, and proposed a mechanism that simply adjusts the damping coefficient, which is the most characteristic of the air suspension. The isefullness of the proposed adjustment mechanism is clarified.
Grant number:16K06148 - Study for friction induced random vibration
Japan Society for the Promotion of Science, Grants-in-Aid for Scientific Research, Grant-in-Aid for Scientific Research (C), 2009 - 2011
YAMAMOTO Hiroshi; ZHENG Ying, Saitama University
Grant amount(Total):4810000, Direct funding:3700000, Indirect funding:1110000
In one degree of freedom vibration systems with frictional surfaces, average amplitude of vibration increases and average frictional coefficients and specific wear rates decrease as a sliding velocity increases. During the frictional surfaces contact each other for long time, the average frictional coefficients and the specific wear rates decrease and the average amplitude of vibration increases. This trend is the same as that of the sliding speed fluctuating.
Grant number:21560233 - Development of Higher Operation Technique in Pulse Detonation Engine (PDE)
Japan Society for the Promotion of Science, Grants-in-Aid for Scientific Research, Grant-in-Aid for Scientific Research (C), 2004 - 2007
OBARA Tetsuro; OHYAGI Shigeharu; YAMAMOTO Hiroshi, Saitama University
Grant amount(Total):3750000, Direct funding:3600000, Indirect funding:150000
In order to obtain higher operation in Pulse Detonation Engine (PDE), it is of importance to get mixing between fuel (hydrogen) and air in a short period, and to ignite, since the detonation wave is produced in a short distance from the igniter. Therefore, the pulse detonation engine was developed which is equipped a rotary-valve and performance of PDE. In this study, experiments are conducted to shorten the detonation induction time by changing a mixing method between a fuel and oxygen, a purge method and injection method of mixing. Conclusions are summarized as follows. 1) A mixing between fuel and air is promoted by decreasing an injection hole, since a penetration distance of hydrogen into the air is increased. 2) Three types of plate to promote the mixing were applied, however the effects of installing plate on higher operation is small. It was found that installing plate method is not necessary from the endurance point of view. 3) The number of fuel injection hole is changed as two and four, thus the two holes is preferable to produce the detonation wave stably.4) In order to shorten the detonation induction distance, the contour of spiral inserted into the PDE is important which is determined from the diameter of the PDE tube. In this study, the detonation induction time is decreased in a case that pitch of spiral is 10 mm.5) The developed PDE can be operated in an operation frequency of 40 Hz. It was pointed out that the PDE tube should be equipped with a cooling method to obtain higher operation frequency.
Grant number:16560134 - Effect of bolted joint layer on the vibration characteristics of high accurate spindle rotor
Japan Society for the Promotion of Science, Grants-in-Aid for Scientific Research, Grant-in-Aid for Scientific Research (C), 2004 - 2005
YAMAMOTO Hiroshi; MIYAJI Ryutaro; ZHENG Ying, Saitama University
Grant amount(Total):2500000, Direct funding:2500000
The effect of joint layer on the vibration characteristics of the hydrostatic gas bearing spindle rotor is investigated. The test rotor is composed of a journal part and two thrust plates bound with bolts. The each surface of bolted joints is processed by two methods in order to change the roughness and the roundness of surface. In all conditions of joint layer, natural frequencies increase and damping ratios decrease as the clamping torque of each bolt increases. On the other hands, in all condition of clamping torque, natural frequencies increase and damping ratios decrease as the roughness and the roundness of surface decreases.
By fabricating the optimum diameter's countersunk hole near the clamping bolt screw hole, the maximum amplitude of the spindle rotor can be decreased because the stiffness and the damping of the joint layer can be increased.
We propose the contact stiffness and damping model of the bolted joint layer of a spindle rotor and the identification procedure of the contact stiffness and damping of the normal and the tangential directions. The contact stiffness in both directions and damping in the normal direction increase as the clamping torque of each bolt increases.
Grant number:16560202 - 溝付き多孔質静圧気体スラスト軸受の動特性に関する研究
1996 - 1996
Grant amount(Total):1000000, Direct funding:1000000
Grant number:08750165 - Developmental Research of Hydrostatic Air Spindle for Ultra-Precision Machine Tools
Japan Society for the Promotion of Science, Grants-in-Aid for Scientific Research, Grant-in-Aid for Developmental Scientific Research (B), 1994 - 1995
ONO Kyosuke; UEMOTO Hiroki; SAI Choshoku; YAMAMOTO Hiroshi, Tokyo Institute of Technology
Grant amount(Total):15300000, Direct funding:15300000
1) Development of the maximized damping design at resonance frequency of bearing-rotor system : Based on the frequency characterisitics of squeeze film damping, we established a design method of maximizing air film damping at resonance frequency of the bearing-rotor system by fabricating the lattice grooves on the radial and thrust bearing surfaces. From this design concept we can increase the damping ratio at resonance up to more than 0.1.
2) Vibration analysis of hydrostatic air spindle including elastic deformation of rotor : Based on the finite element method, we developed the structural modal analysis program of the bearing-rotor system including the elastic deformation of rotor and the equivalent stiffness of the connecting bolts. As a result it is found that not only the three stractural natural frequencies of rotor up to 11 kHz but also air bearing resonances can be predicted more accurately within 5% errors.
3) Development o air spindle design method of minimizing the rms value of rotor response caused by the machining force with various kinds of frequency spectrum : We first determined the radial and thrust bearing configurations so as for the static displacement at machining point to be minimized. Next we developed a design method of compromizing the static stiffness and resonance damping ratio in order to minimize the rms value of dynamic response at machining point. The optimal air bearing designs for narrow and wide band spectrum external forces are exemplified. Further the lowest bending vibration frequency of rotor can be increased up to 7kHz.
4) Realization of ultra-precision air spindle with 10nm/N dynamic compliance in terms of 3 sigma : We made an air spindle prototype whose rms value of the dynamic response is minimized to the imposed machining force with uniform amplitude for the frequencies from 0.5 to 5 kHz. From measurement of the bearing characterisitics, it is found that, because of the machining inaccuracy, the effective bearing clearance is 4 to 4.5 mum, so that the static stiffness is 50 to 70% of the theoretical value for 5 mum nominal clearance. The dynamic air film stiffnesses are larger than the calculated ones by 20 to 30% and the damping ratios are 60 to 80% of the calculated ones. However, it is confirmed that the 3 sigma value of the dynamic compliance of the spindle supported freely can be within 10nm/N in both the radial and thrust directions. It is also found that the rms value of nonrepeatable vibration is less than 10 nm.
Grant number:06555044 - 静圧エアスピンドルのロータ曲げ振動モードの減衰比の向上に関する研究
1994 - 1994
Grant amount(Total):1100000, Direct funding:1100000
Grant number:06750140 - 高減衰静圧エアスピンドルの開発
1993 - 1993
Grant amount(Total):900000, Direct funding:900000
Grant number:05750137 - Development of High Damping Hydrostatic Air Slider
Japan Society for the Promotion of Science, Grants-in-Aid for Scientific Research, Grant-in-Aid for Developmental Scientific Research, 1989 - 1990
YAMAURA Hiroshi; UEMOTO Hiroki; YAMAMOTO Hiroshi, Tokyo Institute of Technology
Grant amount(Total):15700000, Direct funding:15700000
The results of this research is as follows ;
(1) In analysis of one dimensional grooved bearing model, it is found that groove number N_g, depth G and width L_g have little effect on static stiffness at sigma = O. The damping B in low sigma region decreases when N_g, G and L_g respectively become large. But B in high sigma region increases with the increase in G and has an extremum value B_at sigma_ which corresponds to the local squeeze number sigma' of ten in the divided region. We can realize a high damping bearing at resonance frequency by decreasing L_g as small as possible, choosing N_g so as to tune sigma_ to the corresponding natural frequency and increasing G to the limiting value which keeps B positive in low sigma region.
(2) We propose a new hydrostatic air bearing slider with comb-shaped grooves based on the analysis of one dimensional bearing model which can provide high damping ratios at resonances as well as high stiffnesses. The basic idea to increase the air film damping at a high frequency region is to reduce the compressive effect of the air film by comb-shaped grooves. It is found that the zeta of 0.23 can be realized while assuring 0.3 non-dimensional stiffness.
(3)We fabricate a hydrostatic air slider with four comb-shaped grooved beaxings. The fabricated slider has a high static stiffness which is 1.2 times the conventional grooved air bearing's one. Damping ratio is 0.065 which is 2.0 times the conventional grooved air bearing's one.
We can realize the hydrostatic air slider whose damping ratio is above 0.2 if we will realize the higher accuracy clearance and feeding hole diameter and use more rigid material.
Grant number:01850035 - トライボロジー
Competitive research funding - 機械力学
Competitive research funding - Tribology
Competitive research funding - Dynamics of Machinery
Competitive research funding